インサート成形で実現する設計革新(後編):メリットを最大化する設計ノウハウ
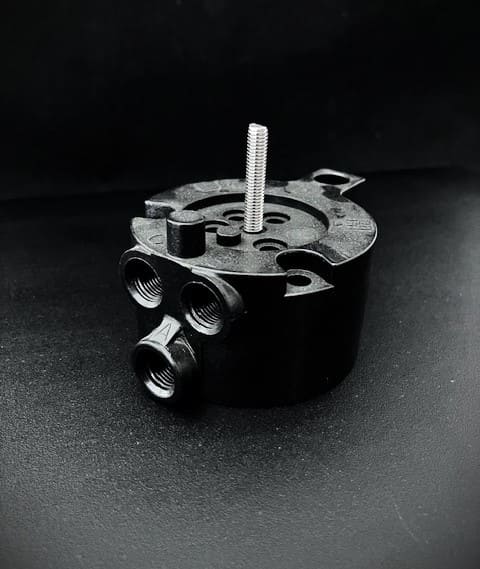
前回のコラム前編では、金型内に金属などの異材質部品(インサート品)をセットし、樹脂と一体化させる「インサート成形」技術の基本と、それが設計にもたらす数々のメリットについて解説しました。特に、劇的なコスト削減(組立工程撤廃、部品点数削減)、製品の高機能化(異種材料の長所活用による強度・耐熱性向上など)、品質・信頼性の向上(強固な接合、寸法安定性)、小型化・軽量化(部品統合、樹脂化)、そして生産性向上とリードタイム短縮(自動化適性、後工程削減)という5つの大きな価値について、具体的な理由とともにご紹介しました。コネクタやモーター部品、センサーケースなどを例に、これらのメリットがどのように実現されるかを見てきました。
また、これらのメリットを実現するインサート成形の基本的なプロセス(インサート品セットから製品取り出しまで)と、成功の基盤となる材料選定の重要性(樹脂とインサート品の密着性、物性、成形性、表面処理など)についても触れました。インサート成形がいかに設計上の課題解決や製品の付加価値向上に貢献しうるか、そのポテンシャルを感じていただけたことと思います。
コラム後編に向けて:設計ノウハウが成功の鍵
コラム前編でご紹介したインサート成形のメリットは非常に魅力的ですが、これらを最大限に引き出し、潜在的な成形不良(インサート品のズレ、密着不良、反り、クラックなど)を回避するためには、設計段階での深い知見と綿密な検討が不可欠です。材料や設備が良くても、設計が不適切では期待通りの結果は得られません。
そこで今回のコラム後編では、インサート成形を成功に導くための核心、「設計上の重要検討事項」に焦点を当てます。インサート品の確実な固定方法、樹脂流動の最適化、強固な密着性を得る設計、応力集中や熱応力への対策など、設計者が直面する具体的な課題と、それを解決するための実践的なノウハウを詳しく解説します。さらに、多様な産業分野でのインサート成形の具体的な応用事例もご紹介し、皆様の製品開発における新たなアイデアのヒントを提供します。コラム前編で学んだ基礎知識を土台に、コラム後編で実践的な設計ノウハウを身につけ、インサート成形の可能性を現実のものとしていきましょう。
設計段階での重要検討事項:メリットを最大化し、トラブルを防ぐ
インサート成形を成功させるためには、製品設計の段階からいくつかの重要なポイントを考慮しておく必要があります。これらを事前に検討することで、後工程でのトラブルを未然に防ぎ、インサート成形のメリットを最大限に引き出すことができます。
インサート品の確実な固定と位置決め設計
成形時の高い樹脂圧力によってインサート品が動いたり、変形したりしないよう、金型内で確実に保持・固定できる構造を設計段階で考慮します(例:インサート品に凹みや穴を設け、金型ピンで固定する)。
インサート品と樹脂部分の相対的な位置精度が重要となる場合は、インサート品の公差、金型での保持方法、樹脂の収縮などを考慮した精密な公差設計が必要です。
樹脂流動設計:充填不良とインサート品へのダメージ防止
ゲート(樹脂の入り口)の位置や種類、サイズを慎重に決定する必要があります。溶融樹脂がインサート品に直接高速で衝突すると、インサート品が変形したり、位置ずれを起こしたりする可能性があるため、衝突を避けるゲート位置や、樹脂の流れをコントロールするゲート設計(例:タブゲート、ファンゲート)が求められます。インサート品の周囲や薄肉部分にも樹脂がスムーズに行き渡るように、適切な肉厚設定と流動性の高い樹脂の選定、あるいはガスベント(金型内の空気抜き)の適切な配置を検討します。ショートショット(未充填)やウェルドライン(樹脂の合流痕)の発生位置と強度も考慮が必要です。
密着強度を確保する設計
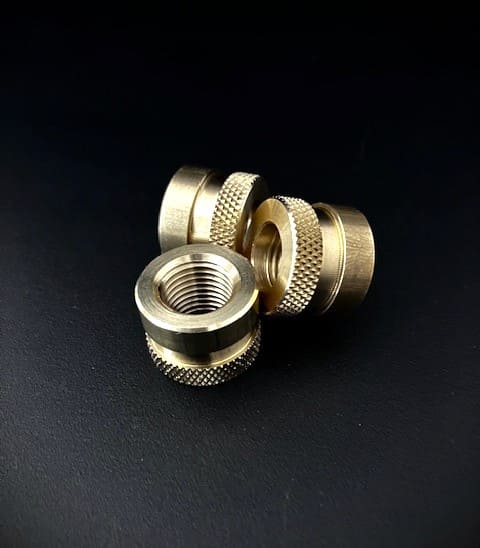
単に樹脂で包み込むだけでなく、インサート品と樹脂との接合強度を高めるための工夫を設計に取り入れます。代表的なのは、インサート品表面に凹凸形状やローレット加工、穴などを設けて、樹脂が物理的に食い込む「アンカー効果」を利用する方法です。
使用する樹脂とインサート品の材質間の化学的な親和性も考慮し、必要であればプライマー処理などの表面改質を検討します。
応力集中緩和設計
インサート品と樹脂の界面、特に角部などには応力が集中しやすく、クラック(ひび割れ)の起点となる可能性があります。インサート品の角部にR(丸み)をつけたり、樹脂部分の肉厚を急激に変化させないように滑らかな形状にするなど、応力集中を緩和する設計を心がけます。
熱応力・収縮差への対策
樹脂とインサート品では、一般的に線膨張係数(温度変化に対する寸法の変化率)や成形収縮率が大きく異なります。成形後の冷却過程で、この差によって内部に応力が発生し、製品の反りや変形、インサート品の破損(特にガラスやセラミック)、あるいは界面での剥離を引き起こす可能性があります。
この影響を最小限に抑えるために、材料の組み合わせを慎重に選定するとともに、応力を緩和する形状設計(例:インサート品周りの肉厚を均一にする)、適切な成形条件(金型温度、冷却時間)、場合によってはアニール処理(加熱・徐冷による内部応力除去)などを検討します。
バリ発生防止のための設計・公差指示
バリ(成形品からはみ出した余分な樹脂)は、外観不良だけでなく、製品機能の妨げになることもあります。インサート品と金型の隙間から樹脂が漏れ出ないように、インサート品の寸法公差を厳しく管理するとともに、金型自体の高い精度と適切な型締め力が必要です。設計段階でバリが発生しにくい形状や構造を検討することも重要です。
金型設計への配慮
製品設計者は、金型設計のことも考慮する必要があります。インサート品をセットしやすく、かつ成形品をスムーズに取り出せるような抜き勾配の設定や、アンダーカット形状(金型が開く方向だけでは抜けない形状)の処理方法(スライドコアなど)を検討します。また、長期的な安定生産のためには、金型のメンテナンス性も考慮された設計が望まれます。
これらの検討事項は、インサート成形の経験豊富な成形メーカーと協力しながら進めることが成功への近道です。
インサート成形の可能性を広げる応用事例
インサート成形技術は、その多様なメリットから、幅広い産業分野で活用されています。ここでは、ターゲット読者の皆様に関心の高い分野を中心に、インサート成形が活用されている代表的な製品事例をいくつかご紹介します。
電気電子機器分野
各種コネクタ:基板実装用コネクタ、電線接続用コネクタなど。金属端子を樹脂ハウジングにインサート成形することで、小型化、高密度化、組立コスト削減を実現しています。フープ成形が多用される代表的な応用例です。
スイッチ・リレー部品:可動接点や固定接点となる金属部品を樹脂製の筐体やレバーにインサート成形し、部品点数削減と信頼性向上を図っています。
スマートフォン・タブレット:筐体の強度確保と薄肉化を両立するため、金属フレームを樹脂と一体成形する例が見られます。
自動車分野
ワイヤーハーネス部品:各種コネクタやジャンクションボックスなど、多数の電線を接続・分岐させる部品で、端子やバスバー(導体棒)のインサート成形が不可欠です。
センサーハウジング:ABSセンサー、温度センサー、圧力センサーなどの各種センサーで、センサー素子や端子を保護するハウジングにインサート成形が用いられ、耐環境性、小型化、コスト削減に貢献しています。
モーター部品:EV/HEV用モーターのステーターやローターの絶縁構造、あるいは小型モーターの整流子やコイルボビンなどで、導体や磁石、シャフトのインサート成形が活用されています。
機械分野
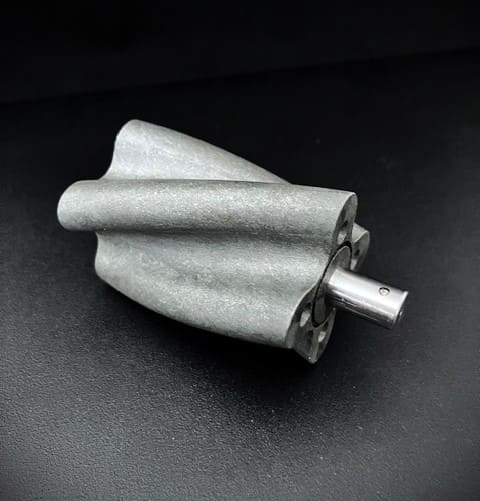
ギア・プーリー:強度が必要な歯部や軸穴部に金属をインサートし、他の部分を樹脂化することで、軽量かつ高強度な動力伝達部品を実現しています。
精密機構部品:産業用ロボットや精密測定器などで、位置決め精度が要求される部品の軸受部や摺動部に、耐摩耗性の高い金属やセラミックスをインサートする例があります。
工具のハンドル・グリップ:金属製の工具本体に、滑りにくく握りやすい樹脂(エラストマーなど)をインサート成形し、作業性と耐久性を向上させています。
流体制御機器分野
バルブ・ポンプ部品:耐圧性が求められるハウジングに金属リングをインサートしたり、耐薬品性・耐摩耗性が要求されるバルブシートやインペラーに特殊金属やセラミックス、高性能樹脂をインサート成形する例があります。これにより、厳しい条件下での信頼性と長寿命化を実現しています。
流量計・圧力計部品:流路とセンサー取り付け部、あるいは表示部などを一体化したハウジングにインサート成形が用いられ、小型化とコスト削減に貢献しています。
これらはほんの一例であり、インサート成形はアイデア次第で様々な製品に応用可能です。
まとめ
本コラムでは、前編、後編の二回にわたり、インサート成形の基礎から応用までを解説してきました。前編では、組立工程撤廃によるコスト削減、異種材料の組み合わせによる高機能化、一体成形による品質・信頼性向上、小型軽量化、生産性向上といった、この技術がもたらす多大なメリットをご紹介しました。そして、後編では、これらのメリットを確実に引き出すための鍵となる「設計上の重要検討事項」に焦点を当てました。インサート品の確実な固定、樹脂流動の最適化、強固な密着性の確保、応力集中や熱応力への対策など、成功には緻密な設計ノウハウが不可欠であることをご理解いただけたかと思います。また、多様な分野での応用事例を読んでいただいたことで、その可能性の広がりを感じていただけたのではないでしょうか。
インサート成形は、従来の設計の限界を突破し、製品に新たな価値をもたらす強力な技術です。しかし、そのポテンシャルを最大限に発揮させるためには、材料、金型、成形条件、そして何よりも製品設計に関する深い知識と経験、そしてそれらを統合する技術力が求められます。本コラムで得た知識が、皆様の設計業務やインサート成形技術の活用検討の一助となれば幸いです。実際の製品開発では、要求仕様の高度化やコストとの両立など、さらに複雑な課題に直面することも少なくありません。そのような場合は、ぜひ、ノウハウを蓄積してきた当社にご相談ください。私たち府中プラは、精密成形やインサート成形を得意とし、設計段階からのご提案、試作、量産まで一貫したサポートを提供しております。インサート成形に関する技術的な課題やお困りごとがございましたら、どうぞお気軽に府中プラまでお問い合わせください。皆様の製品開発を力強くサポートいたします。